オートマタ2号機の制作
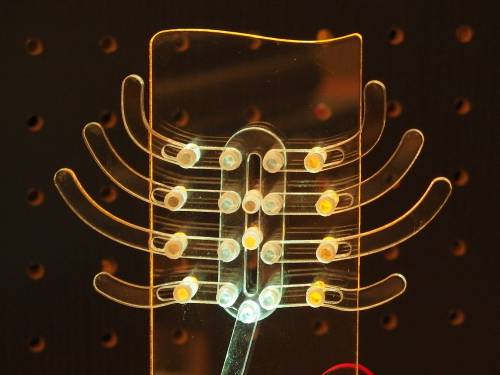
材料にアクリル板を使って作った自転車をこぐオートマタは、レーザー加工機と3Dプリンタを使って比較的簡単に作ることができ、LEDの電飾を組み合わせると透明アクリルの縁が光ってさらに魅力が増します。今回はアクリルのオートマタの第二弾を作りました。
8本足のクモ、エイリアンの幼生といったイメージですが、動きはイソギンチャクといったところでしょうか。
前回オートマタ作成からのフィードバック
構想
設計
各部品の設計(Fusion360)は、本体の機構部分(含ベースプレート)と、LEDを仕込む台座に大きく2つに分かれます。これらは取り外しもできるように、はめこんで固定する構造にします。
本体(機構部分)
設計の手順は、
1枚のスケッチ上に、ベースプレート、動く本体、回転軸を描画。
高さの異なる部品ごとに、押し出し(オフセット)でスケッチから立体化。
動かす部品同士にジョイントを設定し、アニメーションで動きを確認。
必要に応じて部品の形や寸法をスケッチから修正。
設計が出来たら、レーザーカット用に各部品の形をSVG画像に出力。
台座(LED組込み部分)
材料・パーツ
アクリル部品(アクリル板)
前作と同じで、3mm、5mm厚のアクリル板からレーザー加工機で部品を切り出して作ります。
アクリル部品(アクリル丸棒)
技術的な面では今回一番注目していたのが、このアクリル丸棒の使用でした。結論は十分以上に使える材料でしたので、今後も活用していこうと思います。使う上での注意点やポイントといったところもいくつか見えてきました。
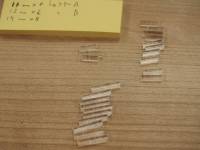
1mの丸棒から1.5cmくらいのシャフトを3種類19本切り出しました。
切断と接着の加工については
別ページに分けました。
PTFE(フッ素樹脂)チューブ
3Dプリンターのプリントヘッドからエクストルーダーの間のフィラメントのガイドに使われたりしている材料です。多少は柔らかさもあって、自己潤滑性もある材料なので、スライドする部品を支えるのにはいいのではないかと思います。
3Dプリント部品
前作オートマタで使用した接続部品と同様の、各パーツ同士を接続するための部品(ストッパー、ワッシャ)です。今回の寸法に合わせて再設計しました。
モーター(ギヤボックス)
前回と同じ、小さく収まり減速比が大きいタミヤのミニモーター低速ギヤボックスを使いました。
LED照明モジュール
PLCコントローラー側から給電して、LED4個(前1個、後3個)を点灯させるモジュールを作成します。組み立てた後からLEDの明るさを調整できるように、電流制限抵抗は外に出しておきます。
導光部品の取付穴にLEDを差し込んで、LED同士は足を曲げて形を整えてはんだ付けします。台座の3層部分の高さ5mmの空間に納めるので、足はLEDの根本に近いところから横に曲げる必要があります。
一方、外に引き出す電線は、被覆のあるもの(取り回ししやすいので、シリコン被覆の柔らかい電線を使いました)を使います。
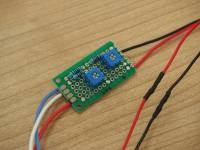
電流制限抵抗は、ユニバーサル基板を小さく切ってその上に組み立てます。
LED①とLED②の2系統の明るさをそれぞれ可変抵抗で調整出来るように配線します。間違えて絶対定格以上の電流を流さないように、固定抵抗と可変抵抗を直列につないだ構成にして、抵抗が一定以上には小さくならないようにします。
組み立て
本体は組み立ての時に力を入れる箇所が幾つかあるので、その際に部品をこわしてしまわないように注意します。台座は粘着剤が部品の表面を汚さないようにマスキングテープで保護します。
本体
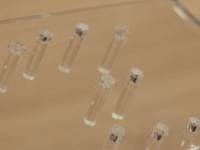
上述のアクリル丸棒の接着にはかなり気を使いました。部品同士のガタツキはそれほどなかったので、接着剤が不要なところに垂れないことに一番気を使って接着しました。
接着後触ってみたところ、3本のシャフトが固定されていません。接着剤がシャフトの断面上に留まったままで、隙間に流れていかなかったようです。再度作業を行って全部接着できました。
余分な接着剤がベースプレートに付いてしまった箇所もありました。ここはコンパウンドを付けて平らに研ぐことできれいに修正しました。
台座
LED照明部分
全体の組み立て
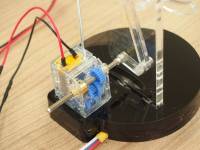
ベースプレートを台座に差し込み、モーターのギヤボックスを台座の四角穴に固定します。このとき、ギヤボックスのシャフトがペースプレートの穴を通るように固定位置を微調整する必要があります。
ギヤボックス内のシャフト固定ネジを一旦ゆるめて位置決めを行い、クランクを取り付けたらネジを締めます。
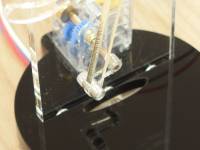
モーター(ギヤボックス)軸とアクリルのクランク部分は差し込んでいるだけです。
断面が六角形の金属の軸を、アクリルをレーザーカットした六角穴に差し込んで、回転を伝えますが、実際に組み合わせてみたらゆるゆるでした。回すことはできているので、少しでもきつくなるようにアクリル専用接着剤を穴の内側に塗っておきました(あまり変わりません)。
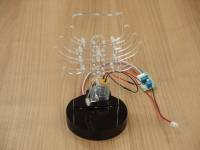
後は固定するのに使った粘着剤が硬化すれば出来上がりです。
テスト運転
モーターとLEDに電源をつないで、設置前の最終テストです。モーターは、本番と同じモータードライバー基板経由でつないでいます。
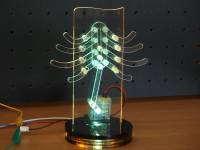
組み立て完成後の最終テスト:モーターによる各部の動きも問題なく、LEDの照明も2色とも明るくついています。
展示
PLCへの組込み
前作の
自転車をこぐオートマタは
2台で展示していましたので、今回はそのうちの1台と置き換えます。コネクターは共通なので、つなぎ替えるだけでいいのですが、コントローラー側の内部配線の変更が必要となります。
前回コントローラーのデジタルOUTの数が一つ足りなくなり、
アナログOUTを準用して対応していたので、配線が他のものと異なっています。今回はその分を新型をつなぐのに使います。
自動運転の
PLCプログラムは、そのままでもよいのですが、もう少し展示物が目立つように、展示スペース全体の人感センサーから信号が入ったらLEDが点灯するように変更しました。モーターを回すのは、従来どおり個別の非接触スイッチがONになったときです。
ラダープログラムの便利なところで、従来のオートマタ用のプログラムに人感センサーからのスイッチの線を1本追加してやるだけで対応できます。実際には、さらに横着して、一緒に点灯する別のLED照明の出力コイルの内部スイッチからつなぎました。これで従来の非接触スイッチからの指示と人感センサーによる指示のどちらに対してもLEDが点灯します。
さらに点灯時間についても微妙に長くなるように見直しました。
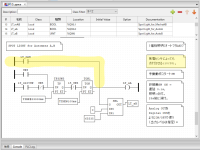
展示スペースへの設置
出来上がった2号機を、展示スペースに持ち込んで、自動運転のシステムに組込みました。
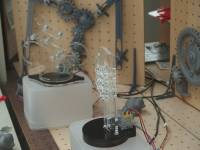
不具合対応
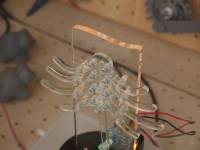
そう思ってキャンドル風LEDを使った今回の2号機に連続供給できる電源を割り当てるべく、オートマタ1,2号機の接続を入れ替えてみたところ、今度は両方のLEDが点くようになりました。めでたしめでたし。
1号機は12Vから10Vに供給電圧が下がったので、電流が減って明るさが減少しましたが、今回は新型の2号機のお目見えなので、そっちの方が目立ってしかるべきです。
感想
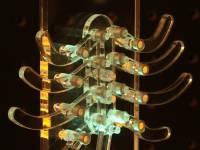
完成して実際に動くのを見ていると、当初の構想よりもきれいで見ていて飽きません。
しばらくこのシリーズを展開させていこうと思います。
-
今後の対応